BX1 Series AC
Arc Welding Machine¡¡
|
The welding-machine of
this series uses move-iron structure, which can weld parts of steel
of low carbon or low alloy. It can be manipulated by only one person.
Compared with ordinary welding machines using natural cooling method, the
BX1-250¡¢BX1-315 and BX1-500 using forcing blast cooling method,
therefore they have such advantages as light weight
and more easily moved than natural cooling welding machine. The welding-machines
of this series can be applied not only to mines or enterprises
but also to medium and small sized repairs. |
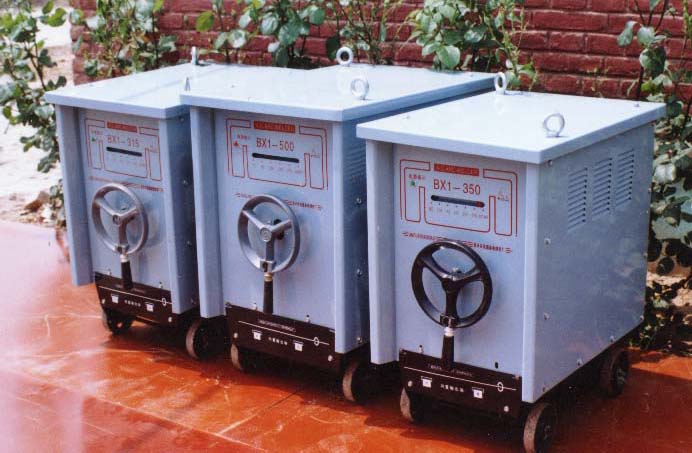 |
First.
attention to safety issues
to
avoid major personal accident, please observe the following :
1.1
Installation, use of the former welder, please read carefully the use of
brochures, and to comply with the warning welder website content and language
warning.
2.2
Please professionally trained and professionally qualified staff to be able to
carry out the welding installation, operation and maintenance.
3.3
The use of cardiac pacemakers, without health care professionals, not close to
being engaged in welding operations and the use of welding. energized the
magnetic field generated by the welding work will have an adverse effect on
pacemakers.
4.4
The non- concerned personnel are not allowed to enter welding worksite.
5.5
Not allowed to work outside the welding machine for welding.
In
order to avoid an electric shock hazard, please observe the following :
Once
exposed live parts may be caused fatal burns and electric shock
1.1
Please do not touch any part of electricity
2.2
Started welding work, should carefully check the importation of power lines to
protect the earth wire and cable insulation and good welding. wiring is correct,
reliable and whether the distribution box and power line capacity to meet the
needs.
3.3
Weld and other protective devices in the demolition of shell off the case should
not be used for welding operation¡£
4.4
The operator must wear protective safety welding supplies.
5.5
Finished welding or welding operations temporarily left the scene, we should cut
off the importation of all welding power source.
6.6
The welder should be regular maintenance professionals.
7.7
Stands as a breakdown of the use of timely inspection, troubleshooting before
you continue to be used.
To
avoid arc welding, flying, welding slag, smoke and harmful gas hazards, the use
of protective equipment
Arc
light will cause eye irritation and skin burns.
Spatter,
welding slag burns to the eyes, skin burns.
The
gentle smoke and dust in air is harmful to your health.
Narrow
places welding operations, Oxygen deficit is able to lead to suffocation.
1.1
During welding operations or observation, monitoring welding operations, the use
of qualified welding wear protective masks or protective glasses.
2.2
Welding set up around the separation barrier in place to prevent harm to others
arc.
3.3
Wear a mask, welding attention to the ventilation exhaust place to prevent the
occurrence of gas poisoning and suffocation.
Especially
in the welding or coated with the coating material, we will create harmful dust
and gases, we must pay more attention to defense.
4.4
Welding in a confined place, the district should arrange for inspections of
ventilation and staff Officers regularly check whether normal operations.
To
prevent fire, explosion, bursting the accident occurred, the following
provisions :
Spatter
from the welding, welding slag, thermal contact with the workpiece will fuel
fire.
power
supply circuit, the welding circuit connecting Department should ensure good
contact, otherwise the work will cause local overheating.
In
the absence of effective preventive measures before the ban in sealed containers
filled with a flammable substance or welding. otherwise it would cause an
explosion or burst.
1.1 Welding worksite is not allowed with flammable, explosive or combustible
materials.
2.2
Connection of the cables will be required reliable and good insulation.
3.3
When the welding or sealed container containing flammable material (such as
pipes, boxes, beds, etc.). have to ask the expert to develop effective
preventive measures can do welding.
4.4
In the welding field should be equipped with the necessary safety equipment,
just in case.
Contact
rotating parts will cause injuries, the following provisions :
1.1 Please do not demolish the shell off, or other protective devices for the
use of welding.
2.2
Not to fingers, clothes, hair and other parts of the rotation near the welder
(such as cooling fan), to prevent injuries.
To
prevent the welding machine and caused fire damage to the insulation properties,
please observe the following rules :
1.1 Welder
placed at the site to ensure welding spatter from the metal powder or other
operations. metal shaving tablets into internal welder, who have found access,
and ensure all of 7659, following the demolition of shell, blowing with
compressed air or other methods to remove the net.
2.2 After
the insulation properties of lead dust accumulation and may even cause an
internal short circuit and affect the normal use of welding, Please light of the
actual situation and send regular maintenance professionals.
Second¡¢welding
machines and the main technical parameters of structural features
main
use :
Weld
way: AC single manual welding arc welding
Major
welding materials : steel, low alloy steel
structural
characteristic:
1.1 Moving
core arc welding transformer, welding current level without regulation, stable
and easy to use.
2.2 IP21
rating for a protective shell, safe and reliable.
3.3 With
the rings, and the wheel to facilitate the use of lifting and moving a short
distance.
4.4 Small
welder(¡Ü200A) a voltage switch, we can use 220 or 380 Overhead voltage.
5.5 Current
and former board equipped with hand wheel adjustment instructions brands, adjust
current convenience.
Main
technical parameters :
Welder
the main technical parameters are listed below
Project
|
Units
|
BX1-160
|
BX1-200
|
BX1-250
|
BX1-315
|
BX1-500
|
Rated
input voltage
|
V
|
Single-phase
380/220
|
Single-phase
380
|
Rated
frequency
|
Hz
|
50
|
Rated
load voltage
|
V
|
60
|
66
|
68
|
72
|
70
|
Rated
welding current
|
A
|
160
|
200
|
250
|
315
|
500
|
Current
regulatory scope
|
A
|
50-160
|
75-200
|
50-250
|
60-315
|
95-500
|
Rated
duty cycle
|
%
|
20
|
35
|
Rated
input capacity
|
KVA
|
10.6
|
13.6
|
18.6
|
22
|
38
|
Insulation
Level
|
|
F
|
Cooling
|
|
Forced
air cooling
|
Dimension
|
mm
|
495¡Á260¡Á425
|
495¡Á260¡Á425
|
390¡Á585¡Á600
|
590¡Á430¡Á720
|
660¡Á493¡Á780
|
Quality
|
Kg
|
39
|
43
|
88
|
98
|
147
|
Basal
principle£º
First. Welding machine electricity principle picture as
follows
Second. The
basic use
The
use of environmental conditions :
1.1 The surrounding
air temperature : -10¡æ
+40¡æ
2.2 Air
relative humidity :
at
+40¡æ in: ¡Ü50%
at
+20¡æ in: ¡Ü90%
3.3 Ambient
air dust¡¢acid¡¢corrosive gases or substances not exceed normal levels, except
for the welding process.
4.4 Not
more than 1000m above sea level.
5.5 Not
suitable for prolonged use in the salt air.
6.6 Welding
supply voltage fluctuations do not exceed the rated input voltage of ¡À 10%.
7.7 Wind
¡Ü1.5m/s the work place.
8.8 Not
suitable for use in the rain.
9.9 Not
suitable for use in the sun for a long time.
welder place :
1.1 Welder should be placed in Steady, less vibration from the walls of not
less than 20cm.
2.2 Welder
should be placed in non-iron, less dust, clean dry place.
3.3 Prevent
rain or water erosion.
welder
link :
1.1 Welder link should be professionals.
The
initial and long-term use of the new place and then re-use the welder welding,
wiring, Application Megger measuring between primary coil and coil, primary coil
and coil insulation resistance between the frame with no low-1M¦¸.
2.2 Welder
and overcurrent protection switches should be equipped with the exclusive
distribution function boxes (board) , with the capacity to be used for welding
match.
3.3 Connection
between the start, has cut off power supply should be recognized.
4.4 Welder
from the distribution box to recommend the use of the order on the beyond-visual
input power cord soft PVC multiple Copper Wire; Another welder output from the
workpiece (grounding clip) and the link between welding tongs should be used YH
or YHF welding or special rubber insulated cables.
5.5 Welder
earthing recommend the use of cross-sectional area of not less than 6mm2
Core; Using Aluminum Core line, recommend the general area of not less than 10mm2.
6.6 We
have to connect the wiring is correct, reliable. Power lines¡¢cable insulation
should be good.
7.7 Welding
supply voltage is same with the input voltage.
The
use of welding
Welder
installed after the link, according to the following sequence of operations
(operations should have received professional training. Welding made for
qualified personnel).
1.1 Check all links are correct, reliable.
2.2 Inspect
power lines, welding cable insulation is good, if damaged, Insulating intact or
be replaced with baling wire insulation good.
3.3 Welding
parts that require inspection, it has serious corrosion, paint or other
substantial impact on the quality of welding fixtures, if any, removals should
be clean, so as not to affect the quality of welding.
4.4 Open
distribution boxes (board) on the power switch.
5.5 Opened
the welder Power Switch (for the use of two voltage of 380 volts and 220 volts
small welding machine, it should be noted that : with the power supply voltage
at the switch), rotating fans.
6.6 Current
regulatory hand wheel rotation (stalk), welding, Current former board
transferred to the corresponding instructions needle position (where the value
of the current instructions for reference).
7.7 The
same with the work piece material on the test welding, welding under test
conditions, the optimum welding current to the best value.
8.8 Implementation
of welding operations.
9.9 Welding
operations disposed of (or temporarily left the scene welding).
10.10 Cut
off the Welder power supply.
11.11 Cut
distribution boards (boards) power.
The
use of attention :
1.1 Actual
needs of the welding current size, will be workpiece thickness, electrode size
and the influence of factors such as welding positions.
Electrode
with a diameter of the welding current relations have shown in the following
table :
Electrode
diameter (mm)
|
Welding
current (A)
|
Electrode
diameter (mm)
|
Welding
current (A)
|
¦Õ1.6
|
25¡«40
|
¦Õ4.0
|
160¡«210
|
¦Õ2.0
|
40¡«65
|
¦Õ5.0
|
200¡«270
|
¦Õ2.5
|
50¡«80
|
¦Õ6.0
|
260¡«300
|
¦Õ3.2
|
100¡«130
|
¡¡
|
¡¡
|
2.2 To
ensure the normal life welder, according to the duty cycle welder and welder to
avoid overload.Weld will set off a serious burn.
Welder
rated duty cycle is a very important technical parameters, Weld said it rated in
the actual welding current work in a welding cycle time (10 minutes) the
percentage.
For
example : Welder rated duty cycle of 60%, which is rated in Taiwan welder
welding current, Welding allowed under six minutes, four minutes and then empty
the recycling.
When
the actual welding welding current is less than the rated current welder,
welding time can be extended.Then load rate calculated by the following formula
:
Allowable
load sustained rate = (Rated welding current ¡Â actual welding ) 2 ¡Á
rated duty cycle
3.3 Be
connected to the welding joint firm, otherwise they will be barred from access
to localized overheating and burning or welding cable connector.
4.4 Welding
cables should not be longer than generally should not exceed 15m.
As a result of actual needs to be lengthened, if welding arc welding current is
too small or difficult situations, C and appropriate cables.
5.5 Welder
prevent rain; To place in cool, dry ventilation, avoid moisture, with iron dust
and placed in many places; In summer, not in
use for long periods under direct sunshine.
6.6 Operators
should wear protective safety complete welding supplies.
7.7 Or
temporary work after leaving the scene, we must cut off the power supply box
welder and distribution.
8.8 Weld
should pay attention to the use of state, found abnormal, should immediately
check stands, remove anomalies can continue its work.
Fourth. The
maintenance welder
1.1 Welder maintenance should be professionals, maintenance before 7659.
2.2 Welder
maintenance should be conducted at least once every six months.
3.3 At
least the following maintenance work should be carried out.
A
Measuring with a Megger between the primary coil and coil. with the primary coil
and coil insulation resistance between the frame must not be less than 1 M¦¸;
B
In addition to using compressed air or brush the dust deposition on the machine;
C
Check whether the connecting link firmly and eliminate all connecting
unreliable;
D
Check whether firmly fixed coils and other components, must be loosened if
solid.
Fifth. General
Troubleshooting
Welder
general breakdown of the causes and treatment methods are listed below :
Fault
|
Cause
|
Exclusion
method
|
Welding
without welding current output
|
1.1
Welder without input voltage input;
2.2
Shedding internal wiring or circuit;
3.3
Internal coil burn.
|
1.1
Distribution boxes to check the switch input welding, wire, Fuse whether
good, solid connection, whether the wiring;
2.2
Weld inspection internal switch, coil wiring is intact;
3.3
Burning the coil replacement.
|
Current
difficulties too small or arc welder
|
1.1
Low voltage network;
2.2
Power lines imported small cross-sectional area;
3.3
Welding cable is too long or too small cross-sectional area;
4.4
A painting dirt workpiece;
5.5
Have access to the workpiece and welding output cables.
|
1.1
To be returned to the rated voltage network after use;
2.2
According to the rated input current welding machine
equipped with sufficient cross-sectional area of the power line;
3.3
Welding cables increase or decrease in cross-sectional Area of welding
cable length of less than 15 meters;
4.4
Weld remove the dirt;
5.5
Good contact with the workpiece output cables.
|
Weld
began.
Burnt
smell emitted smoke or
|
1.1
Welder super load;
2.2
Wrong input voltage or high voltage (220 volts and 380 Overhead available
for the two types of welding voltage, Voltage Overhead wrong by 380 to 220
volts Access);
3.3
Coil internal short circuit;
4.4
Fans will not be diverted; (New welder initial use, a slight varnish
flavor emitted is normal).
|
1.1
Welding work in strict accordance with the duty cycle, to avoid overload;
2.2
Input voltage wiring and the actual operation;
3.3
Check coil, excluding short-circuit fault;
4.4
Fans check and remove Fan Trouble.
|
Welder
big noise
|
1.1
Coil Short;
2.2
Loose coil;
3.3
Moving core vibration;
4.4
Coat or chassis fastening screws loose.
|
1.1
Check coil, excluding short-circuit;
2.2
Check coil s good loose;
3.3
Adjusting screw displacement of the top tight;
4.4
Check fastening screws loose to eliminate the phenomenon.
|
No
cooling fan switch
|
1.1
Fan Connection peeling.
Break or their connections;
2.2
Blade was stuck;
3.3
Fan motor bad.
|
1.1
Fans wiring inspection, troubleshooting;
2.2
Gently pull the fan to check whether rotational flexibility;
3.3
Or replacement of the entire electrical blower.
|
Electrical
shell
|
1.1
Welding cables or power line tour package;
2.2
Welding cable insulation defects collision workpiece
3.3
After the collision loose coil core;
4.4
Collision internal shell or bare wire frame.
|
1.1
Watt, excluding collision shell;
2.2
Inspect welding cable, and wrapped with insulation damaged;
3.3
Check coil, well adjusted and secured the loose coil;
4.4
Traverse internal checks and remove shell collision Department.
|
Six. Randomly
documents
Each
welder at the factory equipped with the following technical documents :
1.1
Use brochures
1
2.2
Certification 1
3.3
Warranty cards. 1
¡¡
|